The unique TorqTrack camera tracking software builds the bridge between mechanical camera support systems and any Virtual Graphics software.
Each movement or rotation axis of your support rig, each parameter of your camera and lens are described in detail to create an exact mathematical model of your physical camera setup.
TorqTrack receives encoder data for each measurement axis of the support system in real-time and feeds it to this model. The virtual camera model simulates exactly the way your real camera moves. The virtual objects seemingly become part of the real environment and vice versa throughout every camera movement with remarkable accuracy.
Perfect immersion of real objects in virtual worlds
Through its high matching precision, TorqTrack supports the illusion of real-life objects, such as persons, furniture, or decorative props to seamlessly blend into the virtual world. Sliding and shifting of real objects in relation to virtual objects can be reduced to a minimum, creating the perfect match for mixed reality setups.
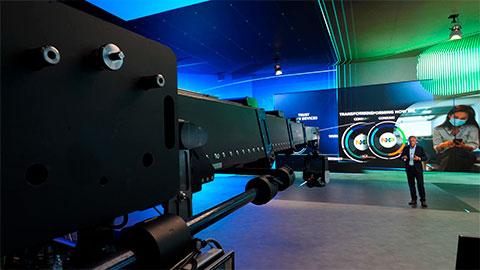

Delivers complete camera tracking data
TorqTrack generates all relevant parameters of the virtual camera model for any camera rig that is equipped with encoders. Whether it is a simple pan-tilt-head or a high-end telescopic crane, you can be sure to have the full set of data for any movement of your camera; besides the position and orientation of the camera, even all lens parameters are generated.
Unique software tools for precise calibrations
To achieve exceptional matching results, it is important to determine all parameters of the virtual camera model precisely. We have designed a unique 3D image processing method for an individual calibration of your applied zoom lens. Using this method, we calculate not only the field of view angle, but also other relevant lens data like distortion parameters, focal distance, and the location of the optical axis regarding the camera’s CCD chip.
To make the placement of a camera support system easier, we have developed RayLocator. This add-on software determines the position and orientation of any support system within a fixed studio coordinate system. With RayLocator, the matching of multiple cameras becomes a piece of cake. But most importantly, you can easily reposition your support system off-air. Meaning, you can find a new position for the support system, remeasure the new position with RayLocator by pointing at some previously installed “landmarks” and go on air again within less than a minute.
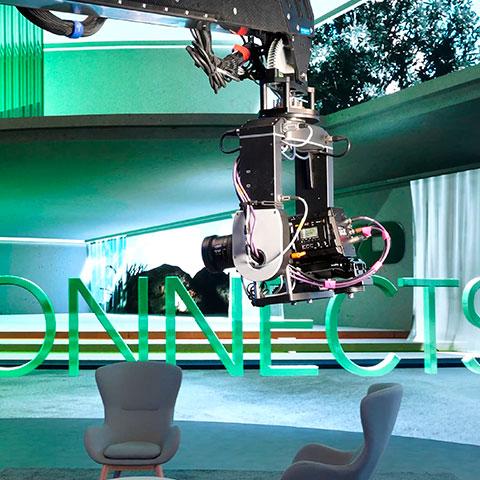
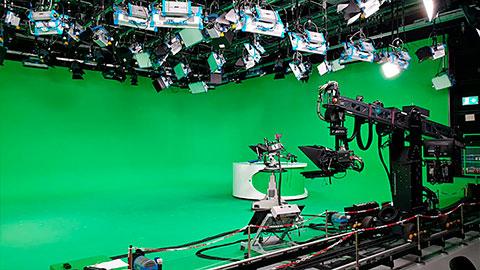
Simple integration of any sensorized support system
Thanks to its open and flexible structural design, TorqTrack works for any support system that is equipped with encoders, any lens, and any camera. It does not matter if your production employs a pan-tilt-head, crane, dolly, tripod, or any other camera support system, TorqTrack supports it.
TorqTrack sends the final camera tracking data via a publicly documented interface to your graphics software. All leading vendors support this interface. The transmission via an Ethernet network allows an unlimited number of graphics clients.
Data flow
TorqTrack receives position data from all moveable axes of the support rig and from the zoom and focus settings of the lens. Based on the mathematical model, the final position and orientation of the camera’s nodal point is calculated. In addition, all relevant lens parameters are generated as well. Finally, all camera parameters are sent over the network to the graphics engines.
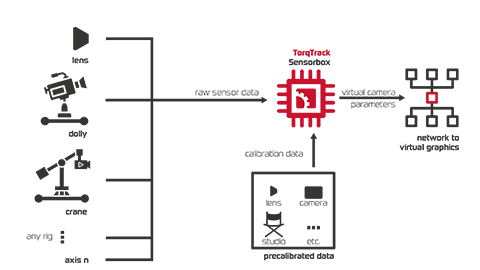
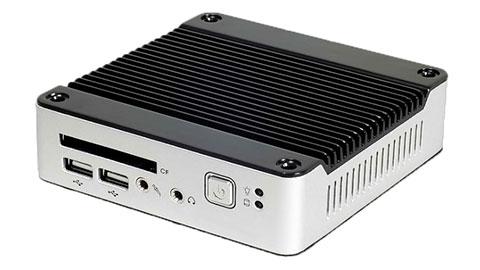
TorqTrack can, in essence, run on any third-party workstation. As a standard, we deliver a miniature computer which receives the mechanical encoder values via network or serial line from any vendor of these mechanical support systems.
To support vendors which provide just the basic quadrature encoder signals but no counter hardware, TorqTrack utilizes a dedicated sensor box which counts encoder signals. It can also receive lens information via serial line or from external lens encoders. The TorqTrack box is synchronized by analogue blackburst or genlock or digital tri-level reference signals.
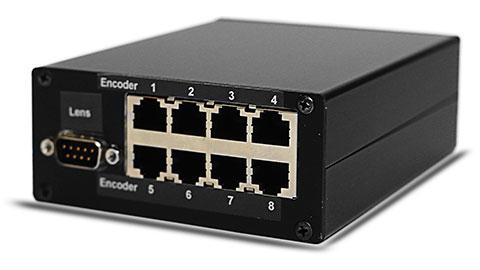
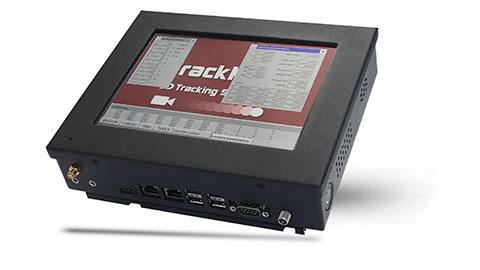
It communicates via USB to a PC. The TorqTrack camera tracking software runs on a touchscreen PC and can be controlled via a graphical user interface. Depending on the individual support system, other hardware configurations might apply.